What are the hazards caused by poor boiler water treatment?
Edit:Qin-Tech Date:2018/8/31 10:58:10 Click:3076
Poor boiler water treatment will cause scaling on the heated surface, greatly reducing the heat transfer efficiency of the boiler, and overheating of the heated surface metal, causing dangerous accidents such as bulging and bursting. Therefore, boiler water treatment is one of the important factors affecting the safety and economic operation of boilers. In addition, poor boiler water treatment can also cause metal corrosion and reduce boiler life. Therefore, doing boiler water treatment work is extremely important for the safe operation of boilers.
First, scaling
After the water is boiled and evaporated in the pot, the chemical reaction and concentration conditions of the impurities in the water are provided. When these impurities reach saturation in the pot water, solid matter is produced. The solid matter produced, if suspended in the pot water, is called slag; if it is attached to the heated surface, it is called scale.
The boiler is also a heat exchange device, and the formation of scale will greatly affect the heat transfer of the boiler. However, the thermal conductivity of scale is only a tenth to a few hundredth of that of steel. Therefore, boiler fouling will cause serious damage to boiler operation.
1. Waste fuel
After the boiler is fouled, the heat transfer performance of the heated surface is deteriorated, and the heat released by the fuel combustion cannot be transferred to the pot water in time, and a large amount of heat is taken away by the flue gas, causing the exhaust gas temperature to be too high, and if the smoke exhaustion is increased, The boiler thermal efficiency is reduced.
In order to maintain the boiler's rated parameters, the company must add more fuel, thus wasting fuel. According to statistics, about 1 mm of scale is wasted a waste of fuel.
2, damaged by the heated surface
In a scaled boiler, the heat of combustion of the fuel cannot be quickly transferred to the boiler water due to poor heat transfer performance, resulting in an increase in the temperature of the furnace and the flue gas.
Therefore, the temperature difference on both sides of the heated surface increases, the temperature of the metal bismuth rises, and the strength decreases. Under the pressure of the pot, bulging and even blasting occur, posing a threat to the personal safety of employees and the property safety of the enterprise.
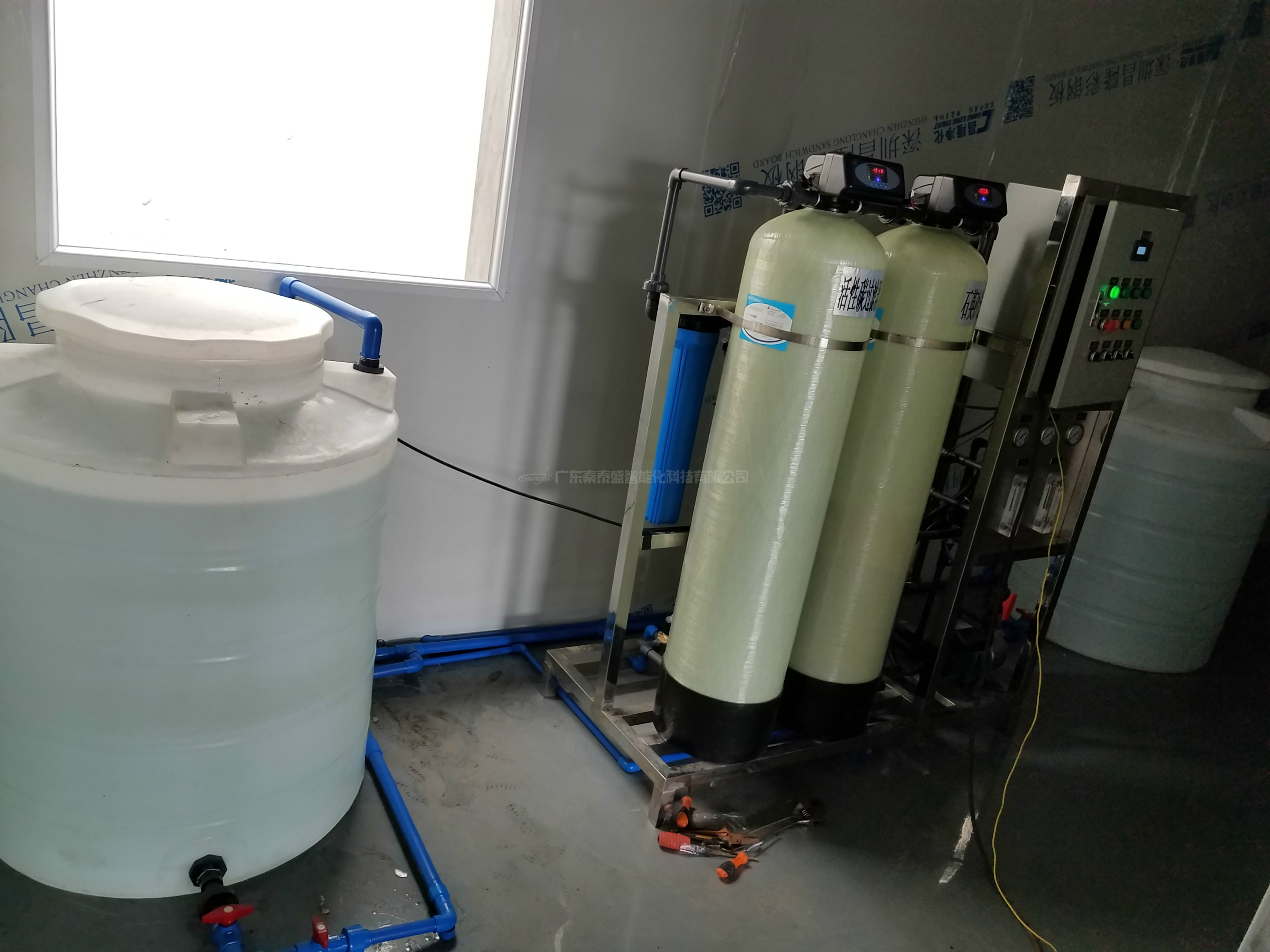
3. Reduce boiler output
After the boiler is fouled, the heat transfer performance deteriorates. Enterprises need to consume more fuel if they want to reach the rated evaporation. However, the volume of the furnace is constant, and as the thickness of the scale increases, fuel consumption is limited. Therefore, the boiler output will be reduced.
Second, corrosion
1. Metal damage
Oxygen, acid and alkaline substances in the water will corrode the metal surface of the boiler, making its wall thickness thin, dent, and even perforated, reducing the strength of the boiler and seriously affecting the safe operation of the boiler. Especially for hot water boilers, the amount of circulating water is large and the corrosion is more serious.
2, under the scale corrosion
Scales containing high-priced iron are prone to corrosion of metals in contact with scale, and corrosion products of iron are easily re-formed into scale, which is a vicious cycle that can quickly cause damage to boiler components. In particular, the metal corrosion products of oil-fired boilers are more harmful.
Third, the soda
The reason for the generation of soda water, in addition to improper operation, is that when the furnace water contains more sodium chloride, sodium phosphate, oil and silicide, or when the organic matter and alkali in the pot water are saponified, During the evaporation process of the pot water, the liquid surface generates foam and forms a soda.
First, scaling
After the water is boiled and evaporated in the pot, the chemical reaction and concentration conditions of the impurities in the water are provided. When these impurities reach saturation in the pot water, solid matter is produced. The solid matter produced, if suspended in the pot water, is called slag; if it is attached to the heated surface, it is called scale.
The boiler is also a heat exchange device, and the formation of scale will greatly affect the heat transfer of the boiler. However, the thermal conductivity of scale is only a tenth to a few hundredth of that of steel. Therefore, boiler fouling will cause serious damage to boiler operation.
1. Waste fuel
After the boiler is fouled, the heat transfer performance of the heated surface is deteriorated, and the heat released by the fuel combustion cannot be transferred to the pot water in time, and a large amount of heat is taken away by the flue gas, causing the exhaust gas temperature to be too high, and if the smoke exhaustion is increased, The boiler thermal efficiency is reduced.
In order to maintain the boiler's rated parameters, the company must add more fuel, thus wasting fuel. According to statistics, about 1 mm of scale is wasted a waste of fuel.
2, damaged by the heated surface
In a scaled boiler, the heat of combustion of the fuel cannot be quickly transferred to the boiler water due to poor heat transfer performance, resulting in an increase in the temperature of the furnace and the flue gas.
Therefore, the temperature difference on both sides of the heated surface increases, the temperature of the metal bismuth rises, and the strength decreases. Under the pressure of the pot, bulging and even blasting occur, posing a threat to the personal safety of employees and the property safety of the enterprise.
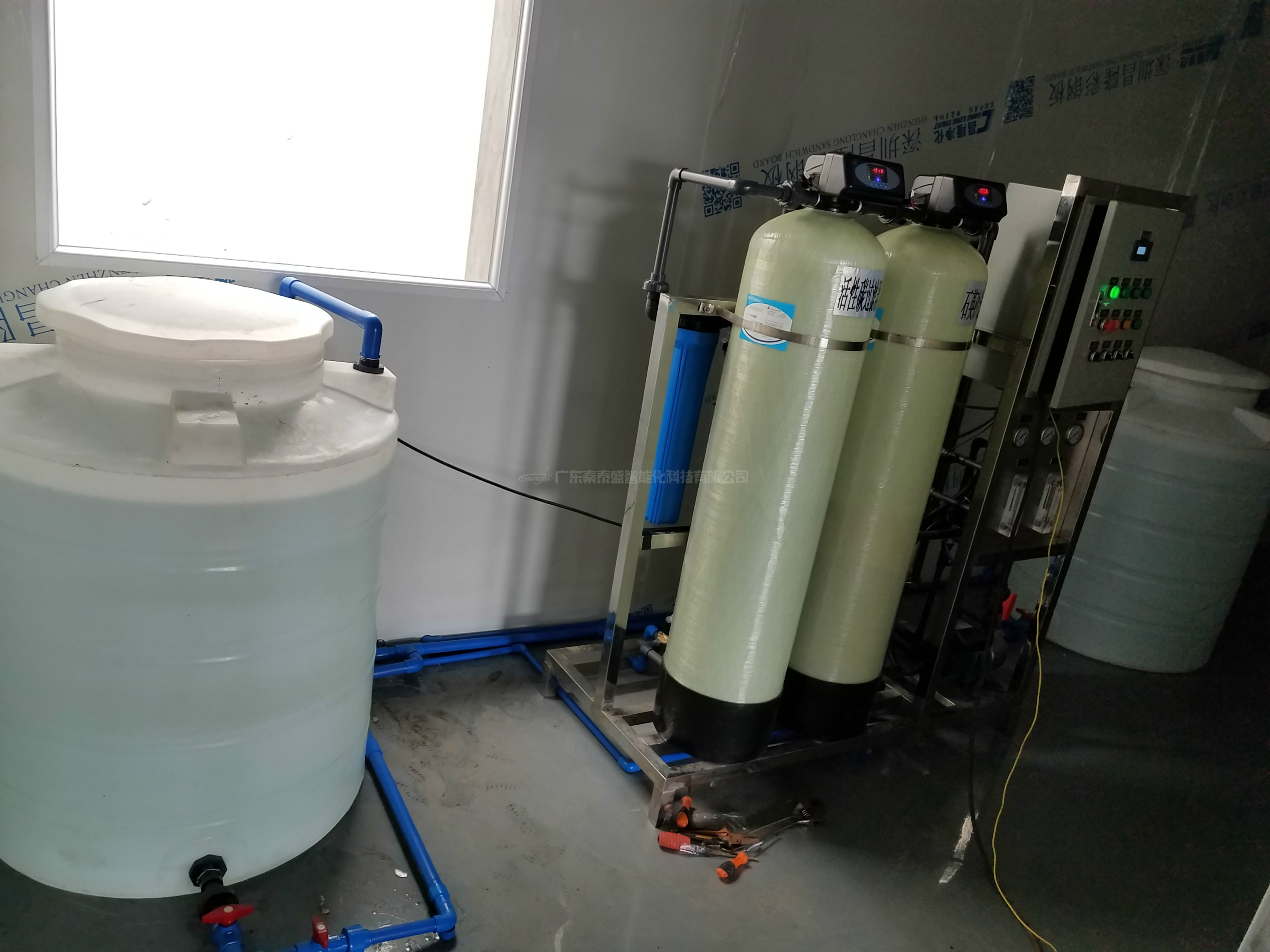
3. Reduce boiler output
After the boiler is fouled, the heat transfer performance deteriorates. Enterprises need to consume more fuel if they want to reach the rated evaporation. However, the volume of the furnace is constant, and as the thickness of the scale increases, fuel consumption is limited. Therefore, the boiler output will be reduced.
Second, corrosion
1. Metal damage
Oxygen, acid and alkaline substances in the water will corrode the metal surface of the boiler, making its wall thickness thin, dent, and even perforated, reducing the strength of the boiler and seriously affecting the safe operation of the boiler. Especially for hot water boilers, the amount of circulating water is large and the corrosion is more serious.
2, under the scale corrosion
Scales containing high-priced iron are prone to corrosion of metals in contact with scale, and corrosion products of iron are easily re-formed into scale, which is a vicious cycle that can quickly cause damage to boiler components. In particular, the metal corrosion products of oil-fired boilers are more harmful.
Third, the soda
The reason for the generation of soda water, in addition to improper operation, is that when the furnace water contains more sodium chloride, sodium phosphate, oil and silicide, or when the organic matter and alkali in the pot water are saponified, During the evaporation process of the pot water, the liquid surface generates foam and forms a soda.
- In the previous:What are the advantages of automatic heat sink adhesive backing machines?
- The next article:How to prevent the reverse osmosis membrane from being contaminated?
Related Reading
- ● What are the hazards caused by poor boiler water treatment?
- ● Automatic industrial boiler softening water equipment features
- ● What if the reverse osmosis membrane is blocked?
- ● Advantages of working with PCB board laminating foam machines
- ● What are the features of a high speed, high precision adhesive backing machine?
- ● What are the advantages of automatic heat sink adhesive backing machines?
- ● Advantages of online automatic backing machine PK manual backing
- ● Detailed features of the automatic camera backing machine
- ● 20 tons of pure water equipment in a food industry in Shenzhen was officially put into production today.
- ● Notice on the Holiday of Dragon Boat Festival in 2022